From time immemorial, man has used two main building materials: wood and stone. Wood attracts with its naturalness, and therefore the installation of a wooden floor has always been a topic that most responsible homeowners are very interested in.
The arrangement of floors in a wooden house or in a brick building has its own differences depending on the architecture and material of the building. But almost all the numerous options for installing wooden floors have their own common features and design features. In particular, almost all such systems are based on jogging.
The purpose of the lag and the requirements for floors and their installation
Any housing should be strong, reliable, durable and convenient for permanent residence. The feeling of comfort, among other things, is created by smooth and warm floors that do not sag under heavy weight and do not creak.
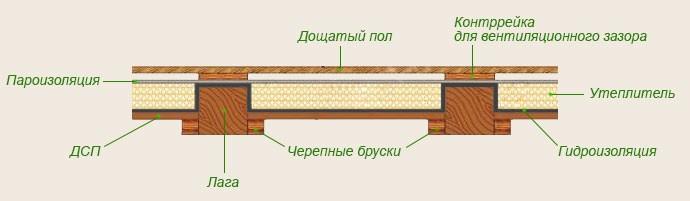
The main purpose of this most important element of the house structure, as well as the specifics of the material from which it is made, impose a number of other requirements on the installation of wooden floors in functional, technical and aesthetic terms. In particular, the floor must be:
- the most rigid and simple in design;
- convenient when laying;
- waterproof;
- resistant to gradual abrasion;
- reliable, durable;
- demonstrating good thermal and sound insulation characteristics, as well as the properties of effective hydro and vapor barrier;
- as fireproof as possible;
- have an attractive design that matches the overall style of the interior.
All these conditions are provided, among other things, due to well-installed lag-mounting elements that act as a support base for laying rough flooring and finishing flooring on them. Most often they are made from wood beams, but in construction practice there are logs in the form of twin boards, wooden slats, metal I-beam channels and even long rectangular plastic products.
As reliable props for the log during the installation of wooden floors, load-bearing structural elements of the structure are used. They can be concrete wall slabs and foundation slabs, embedded crowns, support posts and beams (if the floor is being installed in a wooden house) and even well-compacted soil in advance.
Meanwhile, when the arrangement of the ceiling between the foundation and the first floor of the building is carried out, the question often arises of the legality and necessity of forming a subfloor. This question is especially acute when they make a floor in a wooden house, because of the well-known special relationship of wood to moisture.
Such a space between the surface of the earth and the flooring, exposed on even logs, is recommended to be arranged in the case of a groundwater layer close to the surface. Otherwise, contact with water can lead to accelerated damage (fungal attack, rotting, deformation) not only of the wooden walls of the building, but of the lag bars.
If the groundwater is deep enough, then, for example, for a small country house or a seasonal bath, it will be enough to assemble a simple and cheap (but cold at the same time) floor along logs resting directly on the ground.
Now let's take a closer look at some of the most common floor types.
The simplest cold type floor
Regardless of what material the selected logs are made of, the basis for such a floor must be dry soil.
To ensure suitable conditions, first in the place where the house is planned, it is necessary to remove a layer of soil with all plants. The soil thus opened is well rammed, covered with sand (crushed stone, construction debris) and again carefully compacted.
Calcined sand, dense clay or slag should be used as the next layer of “cushion” for installing a log. They should prevent moisture and subsequent decay of the tree. In this case, the thickness of the insulating layer should be 2-3 times greater than the thickness of the supporting bars. The bars themselves are buried in the backfill layer in such a way that their upper edge protrudes flush with the plane of the base to be equipped.
In order for the loads of the floorboards to be laid to be evenly distributed over the joists, it is recommended to lay the support bars parallel to each other with a step between the joists of no more than 60 cm.
Insulated type of floor laid on the ground
In some cases, it seems appropriate to additionally insulate the floor, the arrangement of which is carried out using the simplest (cold) technology.
To do this, after removing the soil-vegetative layer and before the formation of a multilayer bulk "cushion", the compacted site of the future construction site is covered with thermal insulation in the form of ordinary bags of cement or lime. To obtain high-quality insulation, bags should be covered with at least two layers.
After that, crushed stone is poured onto the bags (a layer 7-8 cm thick). The crushed stone coating is rammed and poured with lime milk. On top of it, a roofing felt flooring is made. This is followed by a layer of fiberboard (thickness - 3 cm) and an 8-cm layer of fine or medium-sized expanded clay.
The formation of the insulating base is completed by pouring "lean" (with a predominance of sand) concrete. After the solution has set, the working area is covered with sand and then work is carried out according to the technology of cold floor equipment.
Cold floor installation with insulated underfloor
This technology does not involve backfilling with calcined sand a surface prepared in a standard way. Instead, under the installation of the lag, support pillars of brick or foam concrete blocks are laid out with a poured foundation for each pillar. Moreover, the edges of the foundation should protrude 2-5 cm beyond the contour of the support column.
It is necessary to ensure that the surfaces of all columns are in the same, strictly horizontal plane. If there is such a need, they are leveled with cement mortar to the level. With the formation of a cement additive with a thickness of more than 5 cm, the layer is reinforced with a reinforcing mesh.
If the installation of a wooden floor will be carried out without additional lathing above the logs, then the logs are oriented so that they are perpendicular to the direction of the floorboard. At the same time, the extreme logs should form gaps with the walls from 3 to 20 cm thick.
All upper planes of the supporting pillars must be covered with a layer of waterproofing. A 3-centimeter wooden gasket is laid out on it, on which the logs themselves are then laid. This gasket, like the logs themselves, should be impregnated with an antiseptic before installation.
Warm floor with cold underground
The device of a wooden floor according to this technology differs from the method described above in that it is not the subfloor that is insulated, but the frame, which is formed by lags.
For this purpose, slats are nailed to the bottom of the wooden bars that are the support for the floorboards. These rails should be attached parallel to each other and perpendicular to the joists. Reiki support the bottom of the insulation panel.
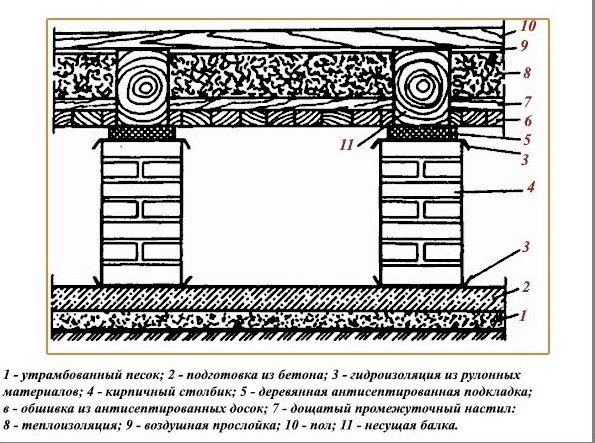
Then the cranial floor thus formed is covered with plastic wrap. Mineral wool or other insulation is laid on the film. At the same time, a small gap must be left between the insulation material and the upper edge of the log for ventilation.
In conclusion, the logs are laid on the floor of wooden boards, which are laid out on a layer of vapor barrier.
Conclusion on the topic
Thus, high-quality installation of wooden floors cannot be attributed to simple installation operations.
If you strictly follow the sequence of actions and perform them carefully and thoughtfully, the task of creating a high-quality floor will be much easier.
More articles on this topic: